top of page
Testing Purpose
The cutting attachment was put through a variety of testing scenarios to see how well it would perform in the hands of Rick and Jeanne when they are using it in their yard. The project had a specific set of device requirements that the cutting attachment was to meet in order to show that the attachment does as it was intended to do. These device requirements were that the attachment:
-
Weighs 10 pounds or less which when added to the impact gun which has a weight of roughly 5 pounds would come in at a weight of 15 pounds or less. This is the lifting weight limit for anyone who is recovering from a surgery such as open heart surgery.
-
Has the ability to cut through a 1-3/8” ± 1/8” diameter tree branch. This diameter is what a standard set of non-ratcheting loppers is rated by the manufacturer to be able to cut through.
-
Has an optional handle with ergonomic hand positioning for comfort of use that the user can attach or detach without tools to help offset the load on a single arm to reduce fatigue on the user.
-
Is made of materials or coated in products that when exposed to outdoor conditions such as rain or other forms of moisture prevents corrosion from occurring as this device will be used in an outdoor setting.
-
Is less than 12” in length from tip of the blades to back of the mounting plate, and 3 1/2” or narrower in width (minus the optional handle), the width of the attached battery pack.”
-
Can be installed onto the impact gun or removed from the impact gun with a single tool in under 5:00 minutes.
Testing Problems
Once the cutting attachment was completed it was mounted onto the impact gun for preliminary testing to see if anything needed to be modified or changed before the main testing began. With a freshly charged battery installed the principal investigator of the project tested out the newly finished tool on a ¾” diameter tree branch and found that it did not have the power or torque to cut through the tree branch. The principal took this problem to professor Pringle to find out what should be done about the problem to remedy a fix. After talking to professor Pringle, Dr. Johnson, and Professor Beardsley it was determined that the torque of the impact gun being used was not at the rated value supplied by DeWALT due to its age. Professor Beardsley came up with a testing rig to determine what the actual output of the impact gun was so the maximum cutting size could be determined. With this rig the principal investigator went over to Geoff Gibson’s garage to perform the test. It turns out that Geoff happened to have the same exact impact gun the cutting attachment was designed for and was only a couple years old and was barely used. At this point the principal investigator mounted up the cutting attachment onto the new impact gun and tested it out. Testing showed that the cutting tool could cut through a 1-1/4” diameter tree branch as it was designed for and testing could begin. The DeWALT DW056 cordless impact gun has an internal brushed motor that does not have replaceable brushes so as they wear out the impact gun loses its maximum torque output. To remedy this problem Rick Hubbard will need to order a new replacement motor and switch out the old motor before using the new tool.
Testing Deliverables
The project testing purpose described above yielded three different types of deliverables to display how well the adapter performed. They are parameter values which are how well the cutting adapter met the parameters set forth for it, calculated values which were values calculated from the collected values to better understand what they mean, and success criteria values which were how well the cutting adapter met the success criteria of the project.



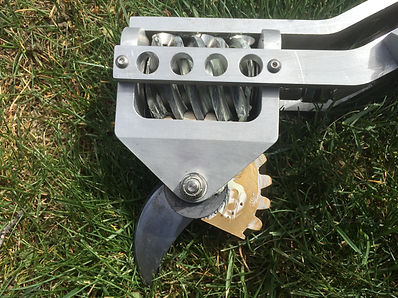

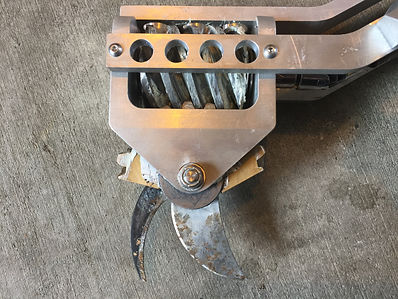





Success Criteria Values:
The cutting attachment met the success criteria outlined by the project and is therefore considered a success by the principal investigator and the requestors of the project. The cutting attachment has made it possible for the user Rick and his wife Jeanne to cut through a branch that has a diameter of around 1-3/8” without exerting excessive stress or becoming fatigued during use. It can also be attached and removed from the impact gun using a single basic tool in under 5 minutes so if the attachment is not already set up the user can quickly and easily prepare it for yard work. As well as it can easily make cuts on a tree branches without the attachments size or weight inhibiting its use.
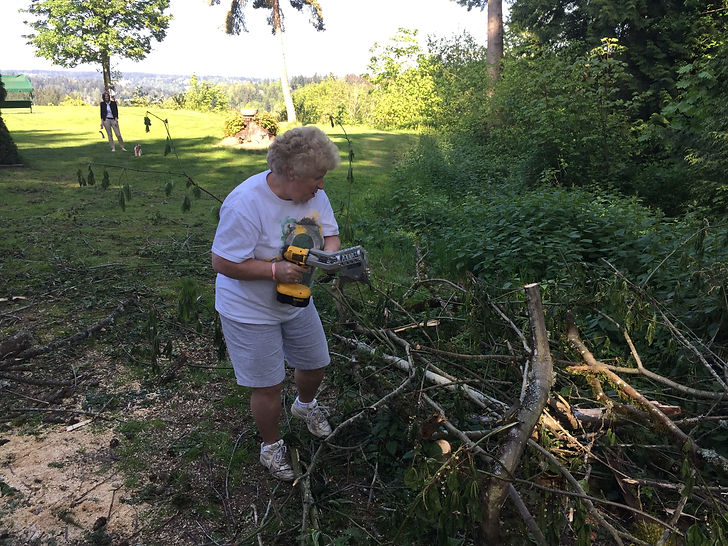
The parameters that are of interest through this testing are the overall size and weight of the cutting attachment. Because this tool is intended to be handheld the size of the attachment is very important to ensure that the user does not become fatigued during its use. The tool is also intended to be easy to use in that the optional handle is intended to be installed and removed without the use of tools to allow the user to use or not use the handle in the yard without having to carry around tools for its install. It was also designed so that the user can install and remove the cutting attachment from the parent impact gun quickly and easily. This is accomplished with a single basic tool so that anyone with any mechanical ability can install the tool and get to work in the yard. The tests will also test the attachments cutting performance on different sizes of branches throughout the battery life of the tool as well as how the attachment holds up to the elements of nature.
Parameter Values:
The cutting attachment met the requirement of being able to cut through a branch with a diameter of 1-3/8” ± 1/8”. This size is the maximum size a pair of non-ratcheting commercial loppers is rated for by the manufacturer. During the speed cutting test the cutter was tested on branches with a diameter of 1-1/4”. This branch size falls into the branch size range listed and therefore passes the test.
Testing Figure 1: Cutting a 1-1/4” branch
Another device requirement was that the cutting attachment was to have an optional handle with ergonomic hand positioning for comfort of use that the user can attach or detach without tools to help offset the load on a single arm to reduce fatigue on the user. The cutting attachment does have an optional handle that requires no tools to install or uninstall from the attachment. Through testing Rick and Jeanne both found the handle to be very comfortable to use and made the tool seem lighter in their hands. Therefore the second optional handle placement is a success because it can be installed and removed without tools and makes the tool more comfortable to use.
Testing Figure 2: Rick showing how easy his new tool is to use
The device requirements stated the cutting attachment is to made of materials or coated in products that when exposed to outdoor conditions such as rain or other forms of moisture prevents corrosion from occurring as this device will be used in an outdoor setting. The device was constructed from aluminum, stainless steel, bronze, and steel. The aluminum, stainless steel, and bronze are resistant to heavy corrosion by nature but the steel is susceptible to corrosion when it comes in contact with moisture. To combat this the blades and steel wormgear were coated in white lithium grease to help prevent heavy corrosion from occurring. Through the weathering testing the blades and wormgear got a slight rust build up on them where the white lithium grease was rubbed off during use. Because the rust did not affect the performance of the tool and was merely cosmetic the tool passes the weathering testing.
Testing Figure 3: Cutter before weathering testing
Testing Figure 4: Cutter after weathering testing
The last parameter value device requirement states that the cutting attachment has a size requirement of less than 12” in length from tip of the blades to back of the mounting plate, and 3 1/2” or narrower in width (minus the optional handle), the width of the attached battery pack. The attachment meets these size requirements measuring in at 10-1/2” in length and 3-1/4” in width. These measurements do not take into account the optional handle and its mounting block. With the handle attached the device length does not change but the width increases to 8”.
Testing Figure 5: Impact gun and cutting attachment on scale
Testing Figure 6: Rick Hubbard removing the cutting attachment from the impact gun
Testing Figure 7: Graph of the time to cut vs. the branch cut number
Testing Figure 8: Graph of the number of cuts per full battery
The smile on Jeanne’s face shows how much she is enjoying her new tool.
Calculated Values:
The device requirements states that the cutting attachment had to weigh less than 10 lbs. which when added to the 4.8 lb. (measured weight) impact gun comes in under the 15 lb. weight lifting maximum for a person recovering from heart surgery. Through Solidworks 3D modeling it was estimated that the completed attachment would weigh 6.1 lbs. Once the cutting attachment was put on a scale it was found that the attachment actually weighed 6.05 lbs. This means that the cutting attachment meets the requirement and gives the cutting tool a final weight of 10.85 lb., 39.5% less than the required maximum weight.
The cutting attachment had a requirement that it could be installed onto the impact gun or removed from the impact gun with a single tool in under 5:00 minutes. The instillation and removal tests were conducted on 4 different people with varying mechanical ability to see how user friendly the attachment is to install onto or remove from the impact gun. Testing found the average install time of the cutting attachment onto the impact gun was 4:13 minutes. This average was a 19.78% difference under the time limit of 5:00 minutes. Testing also found the average removal time of the cutting attachment off of the impact gun to be 3:36 minutes. This average was a 32.56% difference under the time limit of 5:00 minutes. This means that the attachment met this requirement and shows that anyone can install or uninstall the attachment in a reasonable amount of time.
The branch speed cutting test was performed to find out how fast the branch cutter could cut through a branch with a diameter of 1-3/8” ± 1/8”. This was to determine if the tool was a viable option for cutting through tree branches without taking so much time that using the tool becomes tedious for the user trying to do their yard work. It was found that through use the time to cut through a branch steadily increased as the charge in the battery decreased through use and the impact gun lost its level of torque that it could apply. The average cut time for the cutting tool came out to be about 20.8 seconds for a branch with a diameter of 1-1/4” in the conditions tested. This average time will vary depending on the density of the wood being cut and how sharp the blades on the attachment are at the time. Through this testing it was found that the cutting attachment is a viable cutting tool to use as 20.8 seconds is fast enough of cut to not feel tedious by the user.
The last test that was performed which was also not driven by a device requirement was a test to see how many branches the cutting tool could cut on a single battery charge. This would show that the tool could tackle the tasks at hand and would not require the user having to swap out the dead battery for a charged one so often that its use is more of a hassle than the gain the user gets by using it. For this test three trials were run with three fully charges batteries on three different trees. The first two tests were on trees located around Ellensburg WA and the third was on a tree found on Rick and Jeanne’s land in Kenmore WA. Through testing it was found that on around a 1” diameter average tree branch the cutting tool can cut on average 37 branches. This data can be seen in the graph below. This test showed that the cutting tool is a very useful yard tool in that the average person would only be able to cut around 37 branches with traditional loppers before getting tired and the tool tested should have its battery switched out at the same point. This means the cutting tool is on par with the average person but allows them to do the same work with less stress.
bottom of page